
FDY (Fully Drawn Yarn): A Deep Dive into Properties, Production, and Applications
Fully Drawn Yarn (FDY) is a workhorse in the textile industry, prized for its strength, durability, and smooth texture. This article explores the intricacies of FDY, from its manufacturing process and key properties to its diverse applications.
What is FDY?
FDY is a type of polyester yarn that has been fully stretched or "drawn" during the manufacturing process. This drawing process aligns the polymer molecules, resulting in a yarn with enhanced tensile strength, reduced elongation, and a more uniform structure compared to Partially Oriented Yarn (POY). It's a versatile material used in a wide range of textile products.
Manufacturing Process
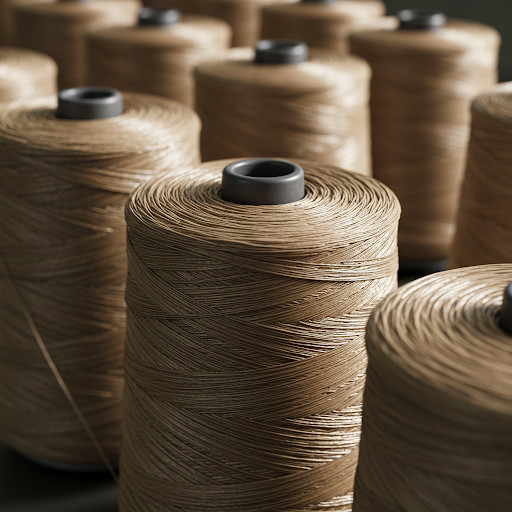
The production of FDY involves several key steps:
- Polymerization: The process begins with the polymerization of propylene, typically derived from crude oil, using a catalyst. This creates polyester chips or granules.
- Melting and Extrusion: The polyester chips are melted and then extruded through spinnerets, which are small nozzles with precisely sized holes. This forms continuous filaments of molten polyester.
- Cooling and Drawing: The extruded filaments are cooled and solidified. Crucially, they are then drawn (stretched) to several times their original length. This aligns the polymer chains, significantly increasing the yarn's strength and reducing its extensibility. This drawing process distinguishes FDY from POY.
- Texturing (Optional): While FDY itself is not typically textured, it can be further processed into Drawn Textured Yarn (DTY) if a bulkier, more elastic yarn is desired.
- Winding: Finally, the fully drawn yarn is wound onto bobbins or cones for packaging and distribution.
Key Properties of FDY
- High Tenacity (Strength): The drawing process imparts excellent tensile strength to FDY, making it suitable for demanding applications.
- Low Elongation: FDY has low extensibility, meaning it doesn't stretch much under load. This contributes to the dimensional stability of fabrics made from FDY.
- Uniform Structure: The drawing process creates a smooth, consistent yarn structure, leading to even dyeing and a desirable fabric appearance.
- Good Dyeability: Polyester, in general, exhibits good dyeability, allowing for a wide range of colors and finishes.
- Abrasion Resistance: FDY offers good resistance to abrasion, contributing to the durability of the final product.
- Relatively High Melting Point: Polyester has a relatively high melting point (around 250-260°C or 482-500°F), making it suitable for applications where heat resistance is a factor. However, it's important to note that prolonged exposure to high temperatures can still cause damage.
Applications of FDY
FDY's versatility makes it suitable for a vast range of applications:
- Apparel: From clothing and sportswear to hosiery and knitwear, FDY is used extensively due to its strength, smooth texture, and ability to hold its shape.
- Home Textiles: FDY finds its way into curtains, upholstery, carpets, and bedding, contributing to the durability and aesthetic appeal of these products.
- Industrial Fabrics: Its high strength makes FDY suitable for industrial applications like tire cords, seatbelts, ropes, and geotextiles.
- Technical Textiles: FDY is also used in various technical applications, including filter fabrics and protective clothing.
FDY vs. POY
The key difference between FDY and POY lies in the drawing process. POY is only partially drawn, resulting in lower strength and higher elongation. POY is often considered an intermediate product that is further processed into FDY or DTY.
FDY is a crucial material in the textile industry, bridging the gap between raw polymer and finished fabric. Its combination of strength, durability, and versatility makes it a preferred choice for a wide array of applications. Understanding its manufacturing process and key properties is essential for anyone involved in the textile industry, from manufacturers and designers to consumers.