
TFO (Twist Filament Yarn): Strength and Versatility in Every Strand
Twist Filament Yarn (TFO) is a type of yarn constructed by twisting multiple continuous filaments together. This twisting process is key to TFO's unique properties, enhancing its strength, cohesion, and texture. This article delves into the characteristics, production, and applications of TFO yarn.
What is TFO?
TFO, as the name suggests, is defined by its twist. Unlike spun yarns, which are made from short staple fibers, TFO yarns are composed of long, continuous filaments (like those found in FDY or POY). These filaments can be made from various synthetic materials, including polyester, nylon, polypropylene, or even silk. The twisting process binds these filaments together, creating a cohesive yarn structure.
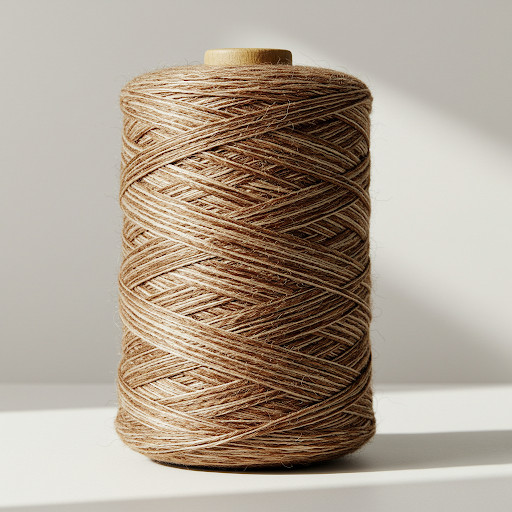
Manufacturing Process
The creation of TFO involves these primary steps:
- Filament Production: The process starts with the production of continuous filaments through melt spinning or other appropriate methods, depending on the type of polymer used.
- Twisting: The core of TFO production is the twisting process. Multiple filaments are fed through twisting machinery, which imparts a specific amount of twist to the yarn. The degree of twist significantly impacts the yarn's properties. Higher twist generally leads to increased strength and cohesion, while lower twist can result in a softer, more flexible yarn.
- Winding: After twisting, the TFO yarn is wound onto bobbins, cones, or other packages for further processing or distribution.
Key Properties of TFO
- High Strength and Durability: The twisting process significantly enhances the tensile strength and abrasion resistance of the yarn, making it suitable for demanding applications.
- Cohesion: The twist binds the filaments together, preventing them from separating or unraveling. This cohesion is crucial for maintaining the yarn's integrity during weaving or knitting.
- Texture Variation: By varying the type of filaments and the degree of twist, manufacturers can create TFO yarns with a wide range of textures, from smooth and lustrous to more textured and bulky.
- Dimensional Stability: TFO yarns tend to have good dimensional stability, meaning they resist stretching or shrinking, contributing to the shape retention of finished products.
- Versatility: TFO can be made from various filament types, allowing for customization of properties like elasticity, dyeability, and heat resistance.
Applications of TFO
TFO's robust properties make it suitable for a diverse range of applications:
- Industrial Applications: Due to its high strength, TFO is often used in industrial applications like ropes, cords, sewing thread, and reinforcement for composite materials.
- Technical Textiles: TFO finds its way into technical textiles such as filter fabrics, geotextiles, and automotive textiles where strength and durability are crucial.
- Home Furnishings: TFO can be used in some upholstery fabrics, particularly those requiring high durability and resistance to wear.
- Apparel (Less Common): While less common than in industrial applications, TFO can be found in some specialized apparel where strength and performance are prioritized.
TFO vs. Other Yarns
- TFO vs. Spun Yarn: Spun yarns are made from short staple fibers twisted together, while TFO uses continuous filaments. TFO generally has higher strength and smoother texture.
- TFO vs. Filament Yarn (without twist): Untwisted filament yarns lack the cohesion and strength of TFO. The twist is the defining characteristic of TFO.
TFO is a versatile yarn characterized by its twist, which imparts strength, cohesion, and texture. Its wide range of applications, from industrial to technical textiles, highlights its importance in the textile industry. Understanding the properties and manufacturing process of TFO is essential for anyone working with textiles, from production to design and end-use applications.